Yankee Scientific: The Practice of Ingenuity
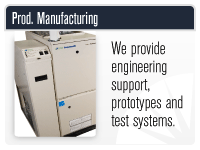
Case Study

High-Speed, multi-axis, computer-controlled machining technology has been the basis for adoption of scroll-type positive displacement compressor technology by several industries. To meet special needs for military power systems, Yankee Scientific developed the technology and tools to create a scroll expanders for generation of power from high pressure steam and gases. Yankee has subsequently designed non-oil-lubricated, non-compliant scroll expanders as well as oil-lubricated, compliant scroll expanders.
Case Study
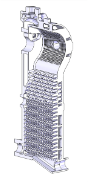
Millions of American homes are heated with steam and hot water boilers made from durable cast iron. For new high efficiency boilers, cast iron is not acceptable on account of the condensation of water vapor in the combustion products. Yankee designed and developed the first cast aluminum boiler produced in the United States. A design particular to the installation practices of the US was conceived that involved the innovative use of single, but complex, aluminum sand casting that integrated the water and combustion passages into a single unit. Production required requiring a minimum post-casting machining for connection of water piping and controls.
Case Study
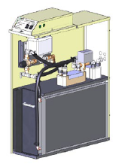
Practical integration of small combined heat and power generation units with conventional home heating systems required the development of a unit that would integrate the mechanical and control functions of the overall system. Yankee completed the mechanical and control design of an Internet communicating Hybrid Integration Module and carried this product through agency certification, field testing, and delivery of production drawings, bill of material, and vendor supply chain to its joint venture partner for mass production.